Introduction
Elion Technologies & Consulting Pvt. Ltd is proud to showcase its expertise in thermography through a recent project with a leading printing company in Solan, Himachal Pradesh. This case study highlights the power of thermal imaging in identifying hidden inefficiencies and optimizing production processes for significant cost savings and improved quality.
Project Overview:
Our client, a renowned printing company known for its high-quality output, was facing challenges with increasing production costs and occasional quality inconsistencies. They sought Elion Technologies’ expertise to identify potential hidden issues within their printing equipment and optimize their overall production process.
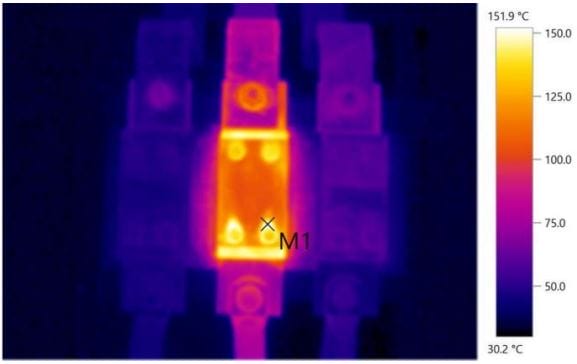
Methodology
Our certified thermographers conducted a comprehensive thermographic survey of the printing facility, utilizing advanced thermal imaging cameras to capture temperature variations across various equipment components. These infrared images reveal heat patterns invisible to the naked eye, allowing us to diagnose potential problems like:
- Overheating components: Bearings, gears, and motors that run too hot indicate excessive friction and wear, leading to increased maintenance costs and potential breakdowns.
- Imbalanced loads: Uneven heat distribution on presses or dryers can indicate inefficiencies in the printing process, affecting print quality and production speed.
- Airflow blockages:Â Clogged filters or improper ventilation can lead to overheating and equipment damage.
- Electrical faults: Loose connections or faulty wiring can generate excessive heat, posing safety risks and potentially causing electrical fires.
Findings and Recommendations:
The thermographic survey revealed several issues within the printing equipment, including:
- Overheated bearings in a high-speed press: Indicating excessive friction and potential wear, leading to decreased press lifespan and increased maintenance costs.
- Uneven heat distribution on a drying unit: Suggesting inefficiencies in the drying process, impacting print quality and production speed.
- Clogged air filters in a ventilation system:Â Restricting airflow and causing overheating of nearby equipment.
- Loose electrical connections in a control panel:Â Posing a potential fire hazard.
Based on these findings, we provided a detailed report with prioritized recommendations for addressing the identified issues, including:
- Replacing worn bearings in the high-speed press:Â To prevent further damage and optimize its performance.
- Adjusting heat distribution in the drying unit:Â To improve drying efficiency and ensure consistent print quality.
- Cleaning or replacing clogged air filters:Â To ensure proper ventilation and prevent equipment overheating.
- Tightening loose electrical connections:Â To eliminate safety hazards and ensure reliable operation.
Results:
By implementing our recommendations, the printing company achieved significant improvements:
- Reduced maintenance costs:Â Avoiding potential breakdowns through preventive maintenance based on identified thermal anomalies.
- Improved print quality:Â Consistent drying ensures optimal ink adhesion and eliminates quality inconsistencies.
- Increased production speed:Â Optimized processes and reduced downtime lead to faster turnaround times.
- Enhanced safety:Â Addressing electrical hazards minimizes risk and creates a safer working environment.
Conclusion
This case study demonstrates the value of thermography as a powerful tool for optimizing printing production processes. By identifying hidden inefficiencies and potential issues before they become critical, Elion Technologies helped this Solan printing company achieve significant cost savings, improve quality, and enhance safety.
Elion Technologies & Consulting Pvt Ltd is your trusted partner for optimizing industrial processes and ensuring equipment reliability. We offer a wide range of services, including thermography, energy audits, predictive maintenance, and industrial safety solutions.
Contact us today to unlock the hidden potential of your operations.